こんにちは、株式会社Key-Performanceの井畑です。
今回は工場などの、複数の行程が合わさって製品を作るときに生じるボトルネック行程について考えます。
ボトルネック行程がある場合、その工場は「間違いなく予定の出荷量を期間中に出荷できなくなる」ので、いち早く見つけ出して解決することが大切です。
そもそも、ボトルネック行程とはなにか??
ボトルネック行程とは、「ラインの中でもっとも作業時間の長い行程」のことをいいます。
基本的に製品の完成時間はこのボトルネック行程の作業時間と同じになります。
では、なぜそんなことが起こるのでしょうか??
なぜボトルネック行程に全体の時間が左右されるのか??
例えば、こんな行程編成のラインがあったとします。
行程1………4分
行程2………2分
行程3………7分
行程4………2分
行程5………5分
このラインでの製品の製造過程を時間を追って見ていきましょう。
最初の製品①が4分で行程1を通過し、行程2に移行します。また、行程1では製品②の製造が始まります。
その2分後に行程2での作業が終わり、製品①は行程2に移動します。しかし、製品②はまだ行程1を通過していないため行程2は作業を行えません。
その2分後(開始から8分後)には行程1から行程2に、製品②が流れます。行程3の作業時間は7分なので、まだ行程4には移れません。
その2分後(開始から10分後)、製品②は行程2の作業を終えました。しかし、行程3では製品①を処理している最中なので、製品②は仕掛品として行程3に残っています。
このまま長々と続けても時間がもったいないので、製品が各行程を通過していく時間を表にまとめました。
この表を見ると、行程1・3と行程2・4・5には明らかな違いがあります。
行程1・4は自工程の作業時間と間隔が一致していますが、行程2・4・5は「上流から流れてくる作業のペースに間隔が左右されています。」自工程の作業時間は反映されていません。
このように、ライン作業では「上流に自工程よりも作業時間の長い行程があれば、その間隔でしか作業を行うことが出来ない」ことが分かります。
そして、「ラインで製品の出来る間隔は、一番時間のかかる行程に左右される」ことも分かります。
この、「一番時間のかかる行程」のことを「ボトルネック行程」といいます。
ボトルネック行程が標準サイクルタイムをオーバーしていた場合
もしこのボトルネック行程が標準サイクルタイムをオーバーしていた場合、絶対に標準サイクルタイム内に製品が出来上がることはありません。
もし目標の製品数を出荷しようとした場合は、工場の稼働時間を増やすしかありません。
なので、ボトルネックの改善は最重要業務になります。
では、改善の仕方を考えていきましょう。
ピッチダイアグラムを使ってボトルネックを発見・改善
ボトルネックの発見と改善には「ピッチダイアグラム」という表が役に立ちます。
ピッチダイアグラムは、各行程の作業時間を棒グラフにまとめたものです。
このピッチダイアグラムを作ると、ラインの改善案がより効果的に見えてきます。
ここでは、改善案の具体例を2つご紹介します。
①:行程3の処理速度を上げる
今回のケースでボトルネックになっているのは「行程3」です。
例えば、行程3に割り振る設備と人員を2倍にしたとします。
この場合、行程3では「7分間で2つ」の処理が行えます。言い換えると作業時間3.5分になりました。
なのでボトルネックが改善され、次なるボトルネックが行程5になります。
ボトルネック行程の処理速度を上げることで解消する事が出来ました。
ですが、これだと割り振る設備・人員・そしてスペースが必要になります。
では、もう1つの改善案をみて行きましょう。
②処理内容を分配する
では、もう一つの具体例です。
先ほどのピッチダイアグラムをもう一度見てみましょう。
このラインでは「行程2・4の処理内容が少なく、行程3の処理内容が多い」事が分かります。
例えば、行程3の作業の「前2分を行程2に、後ろ1分を行程4に」移動したとします。
この場合、ピッチダイアグラムはこのように変わります。
さらに、ついでに行程5の作業の前1分も行程4に移動するとこうなります。
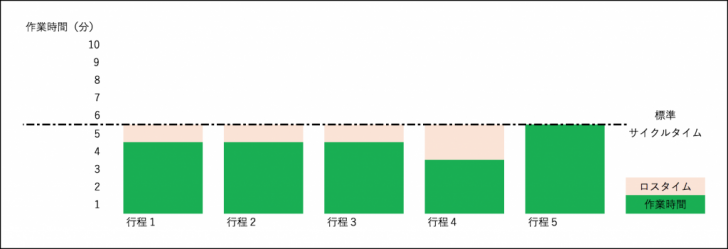
なんと、ロスタイムがゼロになりました。
しかも標準サイクルタイムよりも1分早く製品を作る事が出来ます。
このように、一度割り振った作業内容を再分割することでボトルネックをなくす方法もあります。
※:この方法は必ずうまく行くとは限りません。最初の行程分割の時にすでにある程度の制約の中で組まれた編成ですので、実際にはもっと複雑になります。ただ、もしうまくロスの多い行程に作業を分配出来れば、設備や人員の変更なくボトルネックを解消することが出来ます。
※2:もし今回のように「標準サイクルタイム」よりも短く製品が出来上がってしまった場合、「過剰供給」状態となり売れ残り在庫を抱える可能性があります。その場合は工場の稼働時間に変更をかける等、また別の条件をいじる必要が出てきます。
まとめ
・ラインの行程の中で一番時間のかかる部分を「ボトルネック行程」といい、「製品の製造スピード」=「ボトルネック行程の処理速度」である。
・「ボトルネック行程の処理速度」が「標準サイクルタイム」を上回っていた場合、予定の数の製品を出荷することが出来なくなる。(あるいは、工場の稼働時間が予定より増える)
・ピッチダイアグラムを作ることによって、ボトルネック改善の効果的なアプローチが見える。
[…] 引用元:株式会社Key-Performance […]